CMMS Systems
A significant number of Computerized Maintenance Management Systems (CMMS) are available in the U.S. for factories to manage maintenance processes and timing. Many CMMS software platforms do a very good job focusing on managing and maintaining…
- A detailed list of ‘assets’, their age and specifications
- A work order system to manage maintenance tasks
- A spare parts list
- A proposed maintenance schedule — often based on calendar intervals or machine run-hour data
- Tracking MTBF (Mean Time Between Failures)
However, very few CMMS systems provide any detailed historical machine-operating-data to help plant engineers determine optimum maintenance intervals for various types of equipment, probably because there's no easy way for CMMS firms to capture the necessary data. A SW360 system can fill this data gap and provide engineers with valuable real-time and historical operating information across many machines.
Maintenance Interval Setting
Maintenance intervals in many plants are typically calendar-based — i.e.: “we'll change the oil in the compressors every 6 months”. A better solution is to base it on running hours — “We'll change the oil in the compressors every 2000 hours” — but this doesn't take into account the loads on the compressor(s) for each running hour. It's one thing if the average load over a year is 40% and a totally different thing if it's 85%.
SW360 can provide a much better solution by using real-time operating information — especially load information — for one machine, or a production line, or a whole shop-floor, based on data that our monitoring system can capture on a continuous basis, since higher loading over a period results in more stress on a machine, often leading to shorter ‘Mean Times Between Failures’.
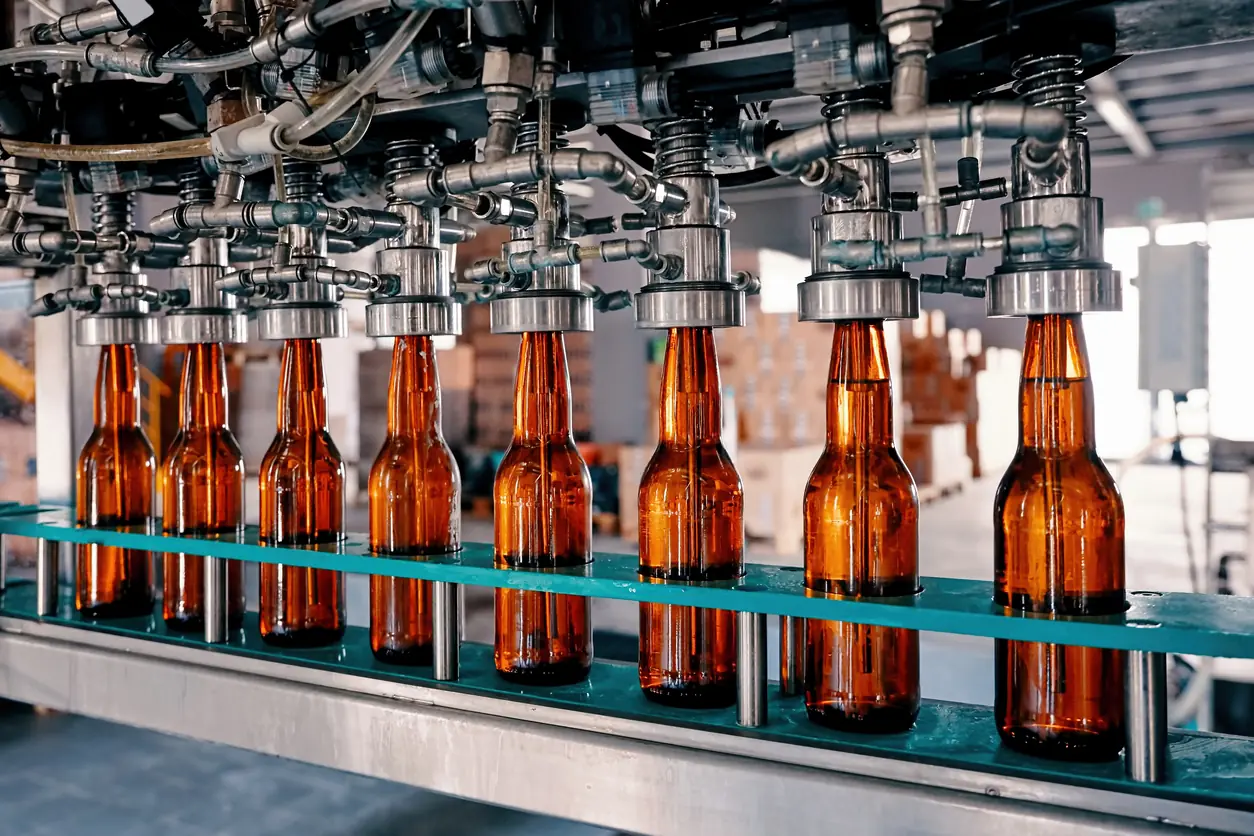
Specific Data Provided
We can provide plant managers, engineers and operators — who may have input into determining maintenance intervals — with at least 12 data sets based on accurate load data we can collect. This data includes both power-use measurements and non-power measurements relative machine-health, such as…
Temperature | Load factor |
Noise | Total power usage |
Vibration | Peak power usage |
Running hours | Time above Full Load Amps |
Load per running hour | # of cycles per hour or day |
Average load | # of stop/starts per shift or day |
SW360 does not give specific recommendations for maintenance intervals for every brand and type of machine, which would be an impossible task. Instead, since customers know their own equipment and processes better than we do, we provide them with real-time and historical data about their machines' workloads and stresses, which they generally have not had access to, until now.
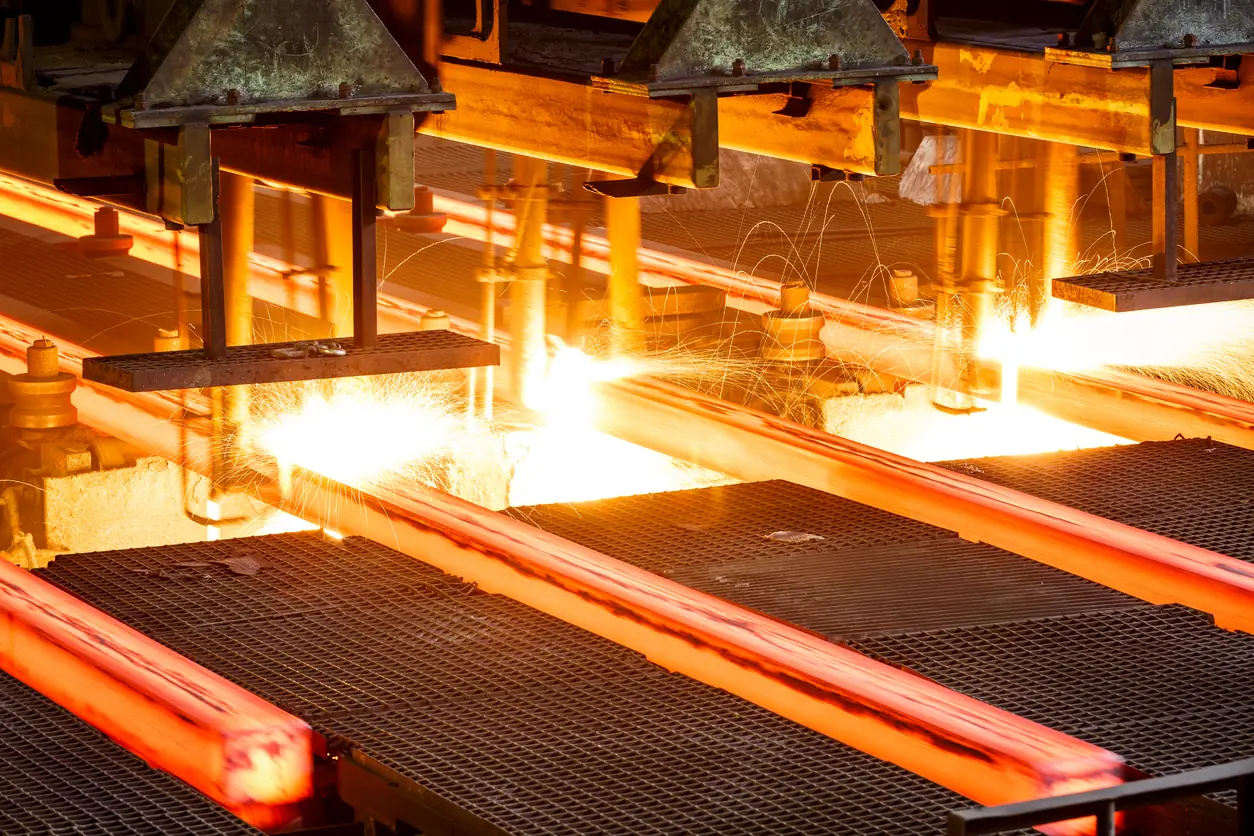
Multi-Variable ‘Compound’ Alerting
In addition to the workload and stress data, customers can use our multi-variable ‘compound’ alerting tool to warn them if any of their machines' operating parameters are moving outside an acceptable range, which the customer can adjust. These alerts can be set to trigger if only one variable moves out of range for a certain amount of time, or to trigger if 2, 3, 4 or more conditions occur simultaneously. Most significant failures in business occur because several contributing factors combine to cause a catastrophe! Here are two examples…
- A water-cooled chiller. If the power draw of the chiller moves, say, X% higher than it's normal operating range and/or the cooling water temperature rises by Y% and/or the water-flow drops by Z% and/or a cooling tower fan has stopped working.
- An injection molding machine might experience heater-band failure, hydraulic pump failure, extruder failure, pellet delivery failure, air dryer failure, lack of air pressure etc. Our compound alerts can be set to trigger if one condition or multiple conditions occur.
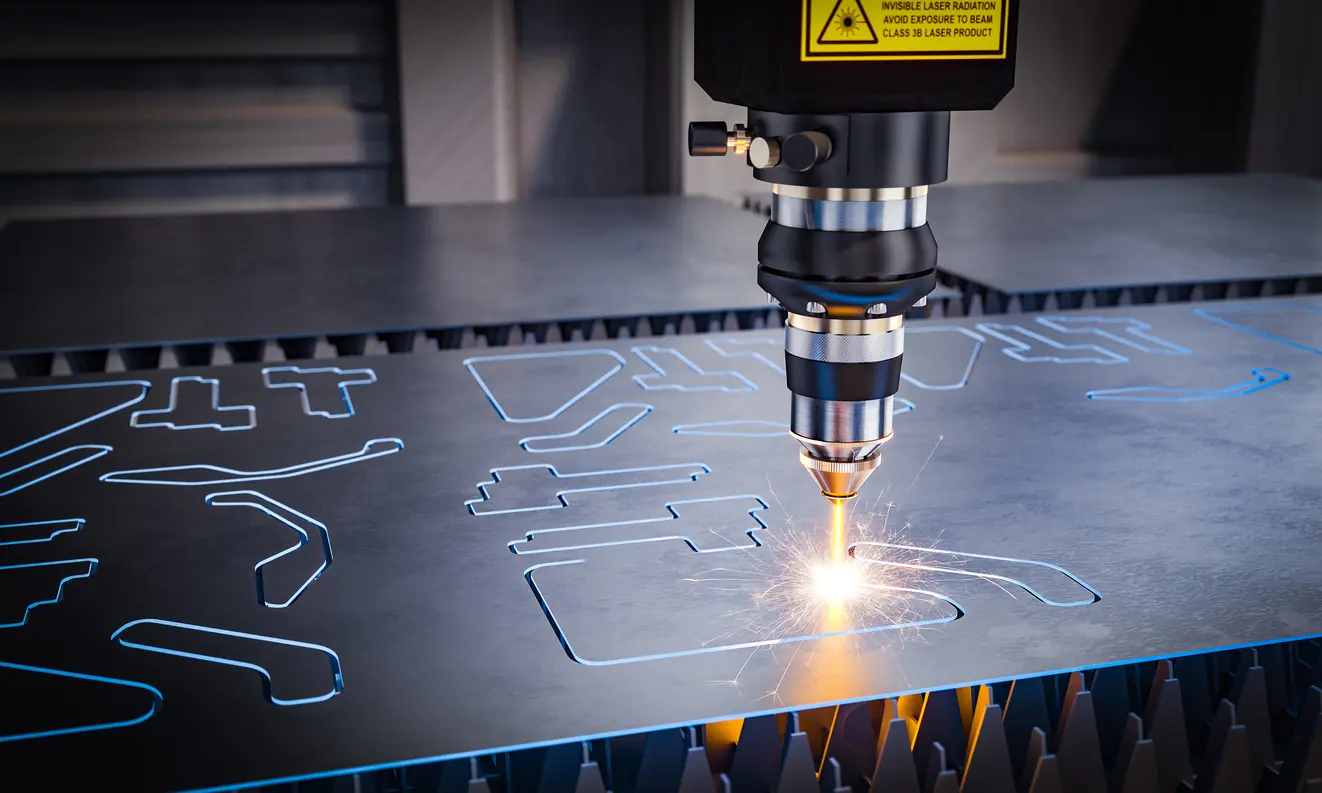
Of course there must be measurements captured for each variable. Alerts won't work without the necessary sensors, meters (or PLCs if connected). If such sensors or meters are not installed, our engineers can help customers select the best options and install them.
All of our data, including alerts, can be exported to standard CMMS systems or any other system.
FAQ
Yes, SW360 can alert you if one machine or multiple machines are operating outside their normal power-draw range(s).
SW360 provides detailed data that helps you move from calendar-based to predictive or condition-based maintenance. The optimum interval for maintenance procedures for any given machine depends on the kind of work the machine performs, the number of hours it runs and the load on the motor for each running hour. 6000 hours of operation at 90% of full load is very different from 30% of full load, resulting in a lot more stress and a higher likelihood of machine deterioration over time. Clients typically use our data to support, rather than replace, manufacturers' maintenance guidelines.
SW360's Maintenance Interval Guide provides data concerning machine running hours and loading.